
Tooth profiles (A0, A1, and A2) of the theoretical cycloidal gear a0... Download Scientific
Friction: Involute gears normally mesh with 2 or 3 teeth in contact at the same time while cycloidal gears can be designed so that only 1 or 2 teeth are in contact at a time. Because some sliding contact occurs in all gear designs, involute gearing will tend to have more friction that a comparable cycloidal design.
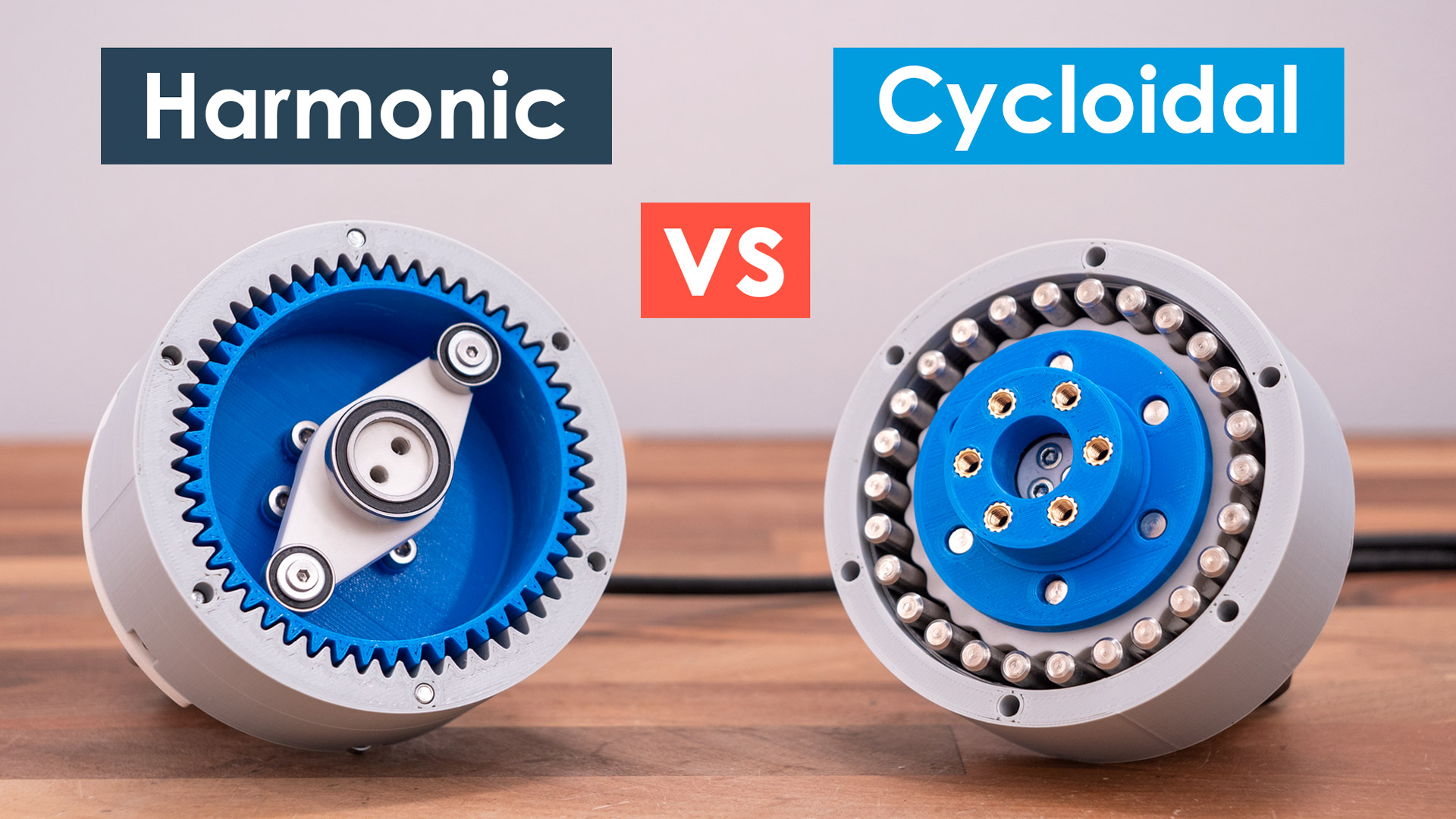
Harmonic vs Cycloidal Drive Torque, Backlash and Wear Test
Engineering. Nabtesco's Cycloidal Gear technology is the far superior choice when compared to traditional planetary and cam indexing devices. The Nabtesco Reducer consists of a patented two-stage cycloidal design that provides large torque, high-ratio and significant shock-load capabilities with extreme precision and excellent quality.

Mechanical notes Machine Drives ( Gear Drives ) (13) ( Comparision between involute and
Step 1: Find the Motor RPM. If you're wondering how to find gear ratio for our Cyclo, you'll need the motor RPM. To calculate this gear ratio, let's use a Cyclo 6000 that has 1800 RPM at the VFD. Step 2: Find the Final Output RPM. The next most important piece of the gear ratio equation is the final output RPM of the industrial gearbox, as.
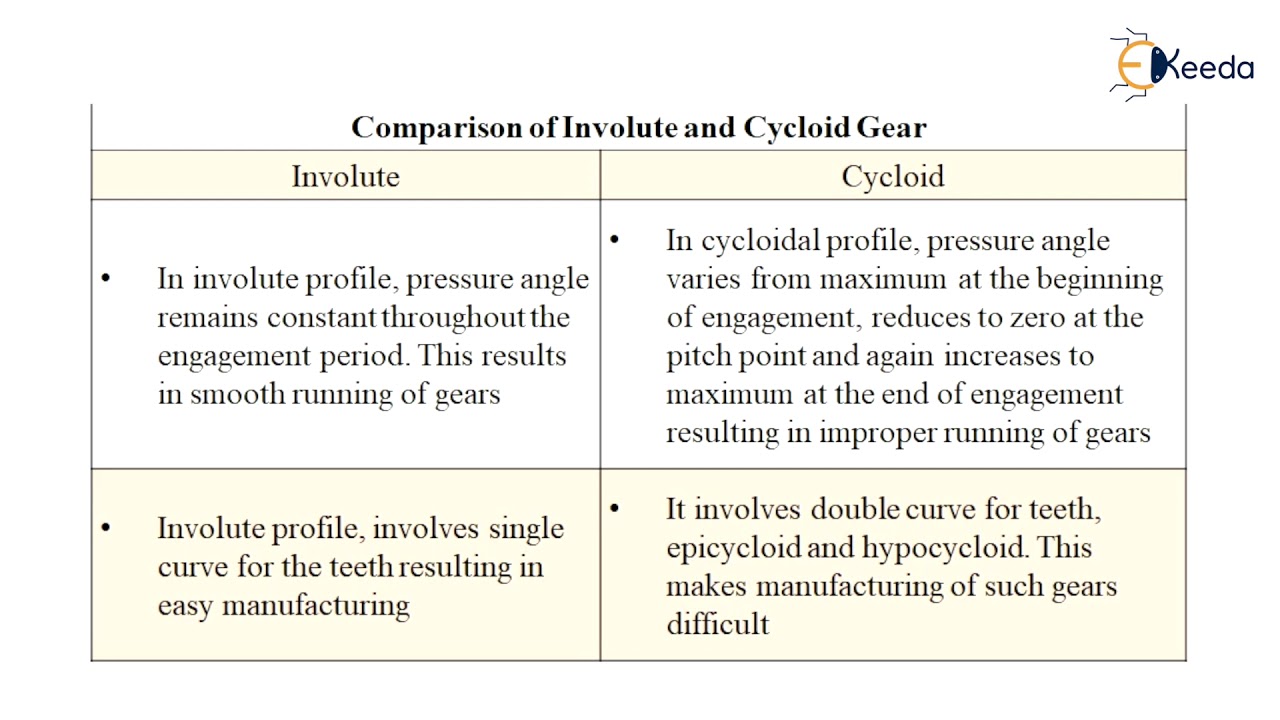
Comparison of Involute and Cycloidal Gear Design of Spur, Helical, Bevel and Worm gear and Gear
In a hypocycloid (or simply cycloid) speed reducer, a flower-shaped gear called cycloid disk moves around a stationary ring of round pins in a cycloidal motion, driven by an eccentric bearing or cam connected to the input shaft. Radial holes on the face of the cycloid disk in turn drive the pins of the output shaft. The cycloid disk is the most.
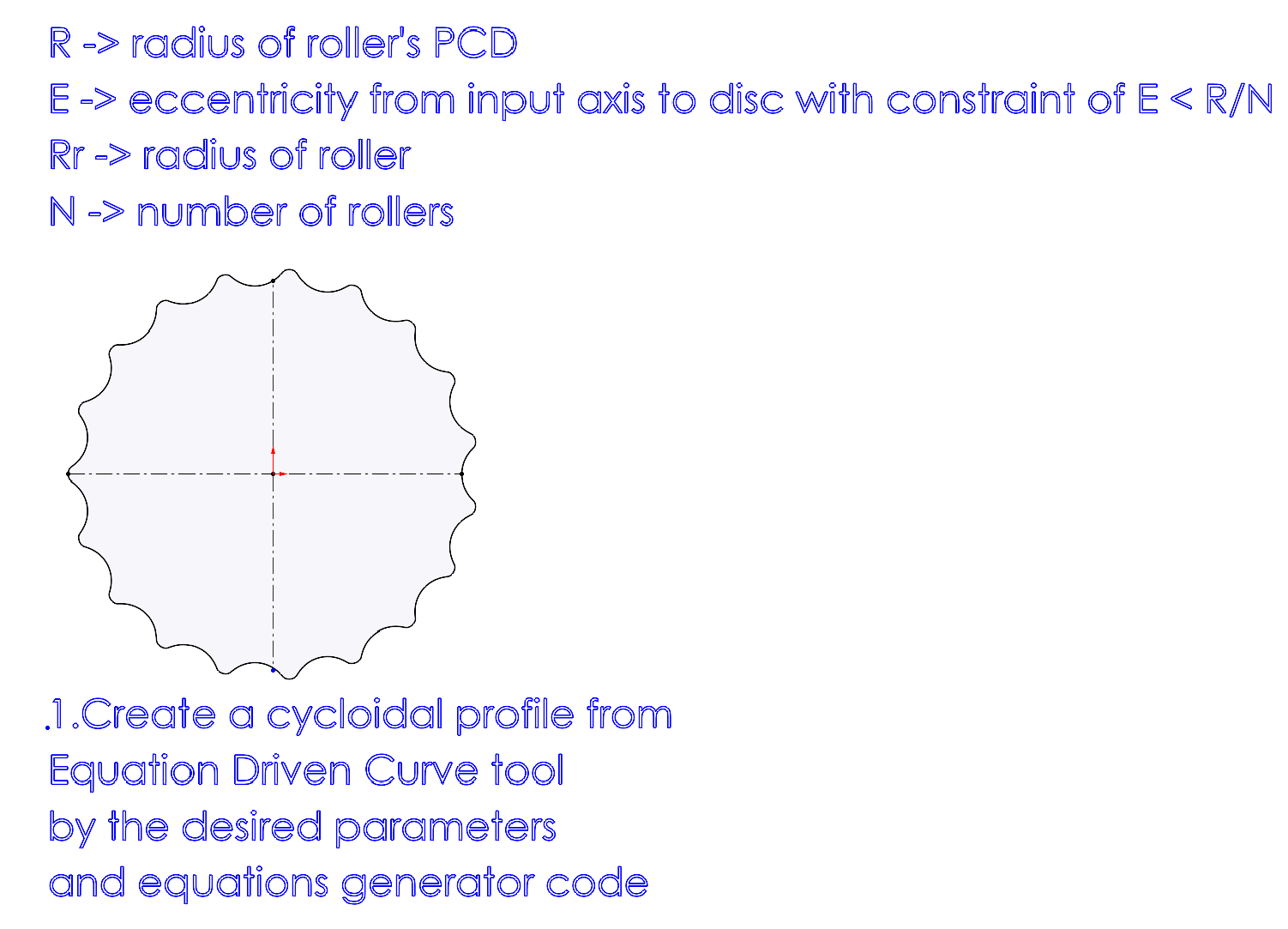
Cycloidal Drive StepByStep Robotics
Cycloid gear graphic calculator. This is a little utility to help in the design of cycloidal drives. It is a port to C# of this python script. with some added features (mainly, the graphical display). This is some quick code I put together one day, but is contains a nice design that allows for easy visualization of any complex formula, so it is.

Dr Rainer Hessmer
I did however find Hugh Sparks' excellent write-up on cycloidal gears and the associated JavaScript based calculator. The calculations reflect the British Standard 978, Part 2.. It looks like you may not be monitoring this blog any more, but in case you happen to see this, the "cycloidal gear builder" is a really nice program, thank you.
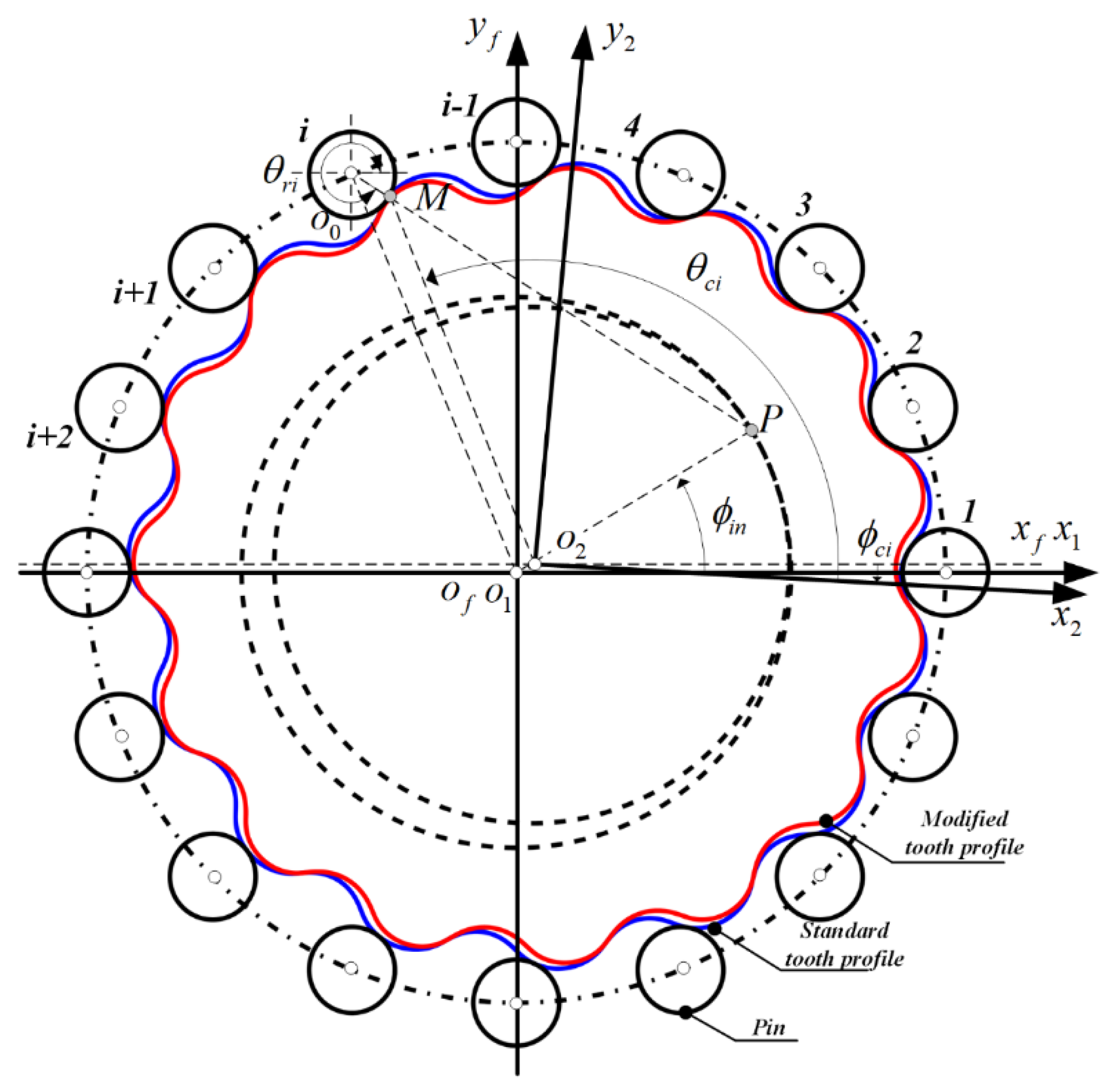
Applied Sciences Free FullText A SemiAnalytical Load Distribution Model for Cycloid Drives
The compound reduction cycloidal gear train handles all ratios within the same package size, so higher-ratio cycloidal gear boxes become even shorter than planetary versions with the same ratios.
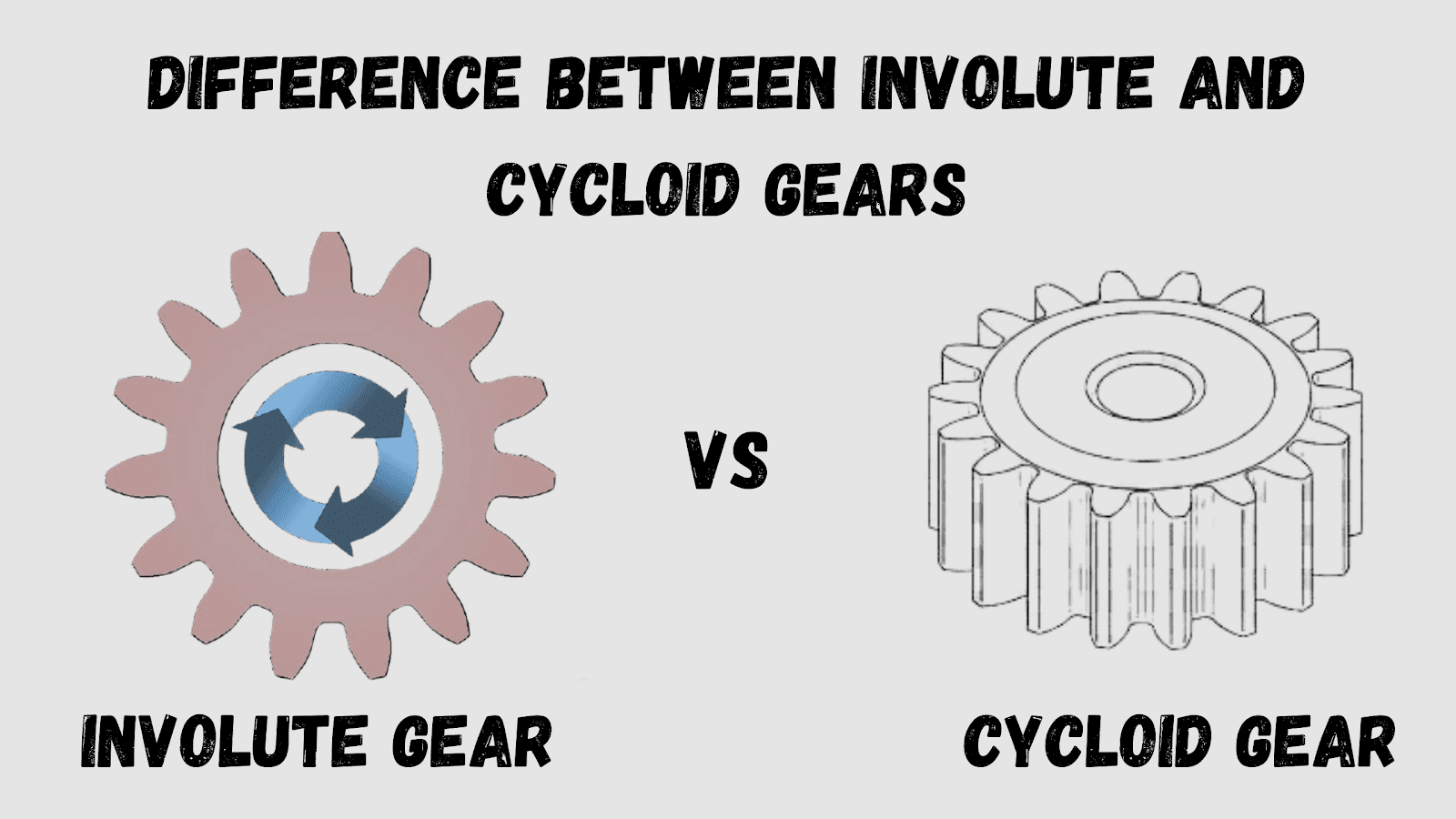
Difference Between Involute And Cycloid Gears? Mechanical Education
How to Design an Eccentrically Cycloidal (EC) Drive. How to Design and Test the Automotive Differential in Blender.. Involute Gear Calculator. The following online calculator computes the basic dimensions and tooth profile of an involute gear based on its module, number of teeth and pressure angle (the latter is usually 20°)..

Designing epicycloid gears a, b) uncorrected gears internal and... Download Scientific Diagram
Cycloidal drive vs. planetary gear. When it comes to large transmission ratios in a compact design, two gear types are particularly suitable: The planetary gear and the cycloidal drive. The similarities between the two gear types become particularly clear when the ring gear of the planetary gearbox is fixed. The gearbox is driven by the sun.

The four types of tooth profile modifications for cycloid gears. Download Scientific Diagram
Cycloidal Gear Calculator British Standard 978, Part 2. Module: mm Number of wheel teeth: Number of pinion teeth: Circular pitch: mm Dedendum: mm Gear ratio: Addendum factor: Addendum:. Dr. Rainer Hessmer's Cycloidal Gear Builder.
Solved Designing a cycloidal gear help PTC Community
Online Cycloidal Gear Builder. Almost exactly a year ago I published a blog post introducing an open source application for calculating cycloidal gears. The response was very positive but the fact that the tool depends on a specific version of .Net makes access a bit cumbersome. Also the tool does not immediately show the resulting gears.

How does a cycloidal drive work? tecscience
The calculations reflect the British Standard 978, Part 2. They are based on Hugh Sparks' excellent write-up on cycloidal gears and his associated JavaScript based calculator. Instructions. Specify desired values in the parameters box and then click on the 'Update' button. Dependent on the specified resolution the rendering might take some time.
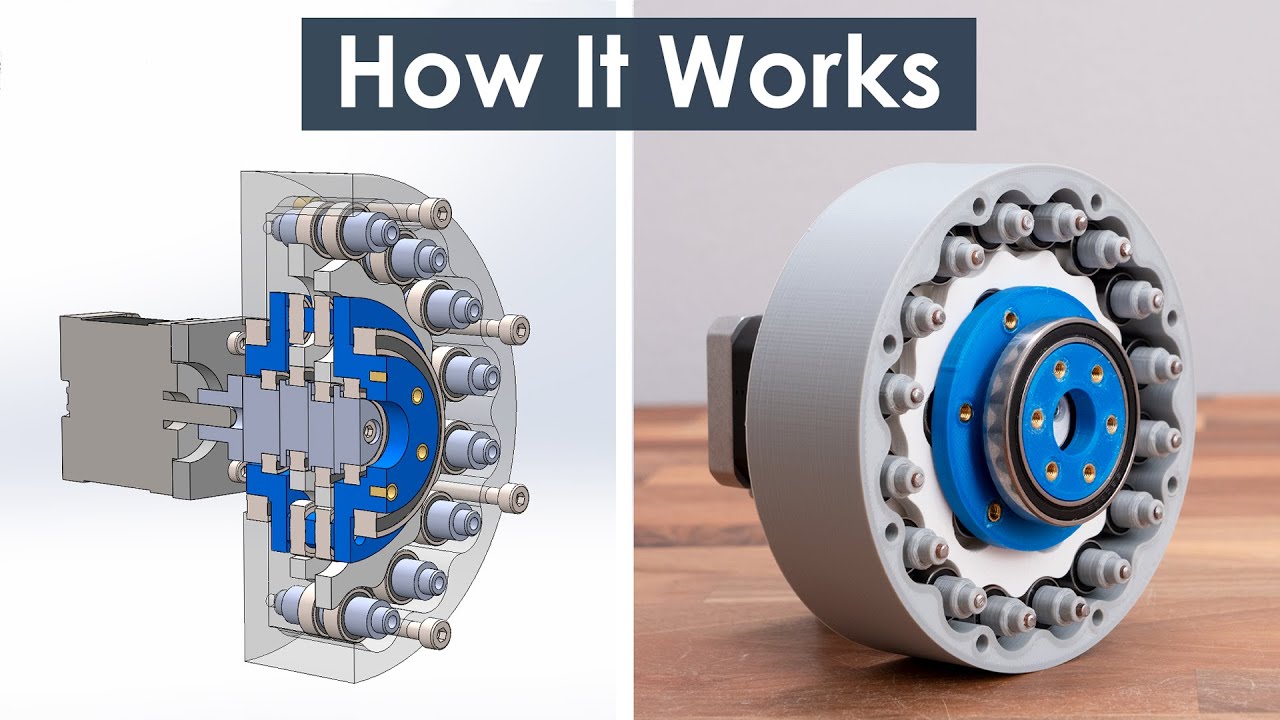
What is Cycloidal Drive? Designing, 3D Printing and Testing YouTube
Construction of a cycloid. The shape of the flank of a cycloidal gear is a so-called cycloid. A cycloid is constructed by rolling a rolling circle on a base circle. A fixed point on the rolling circle describes the cycloid as a trajectory curve. A distinction can also be made between an epicycloid and a hypocycloid.
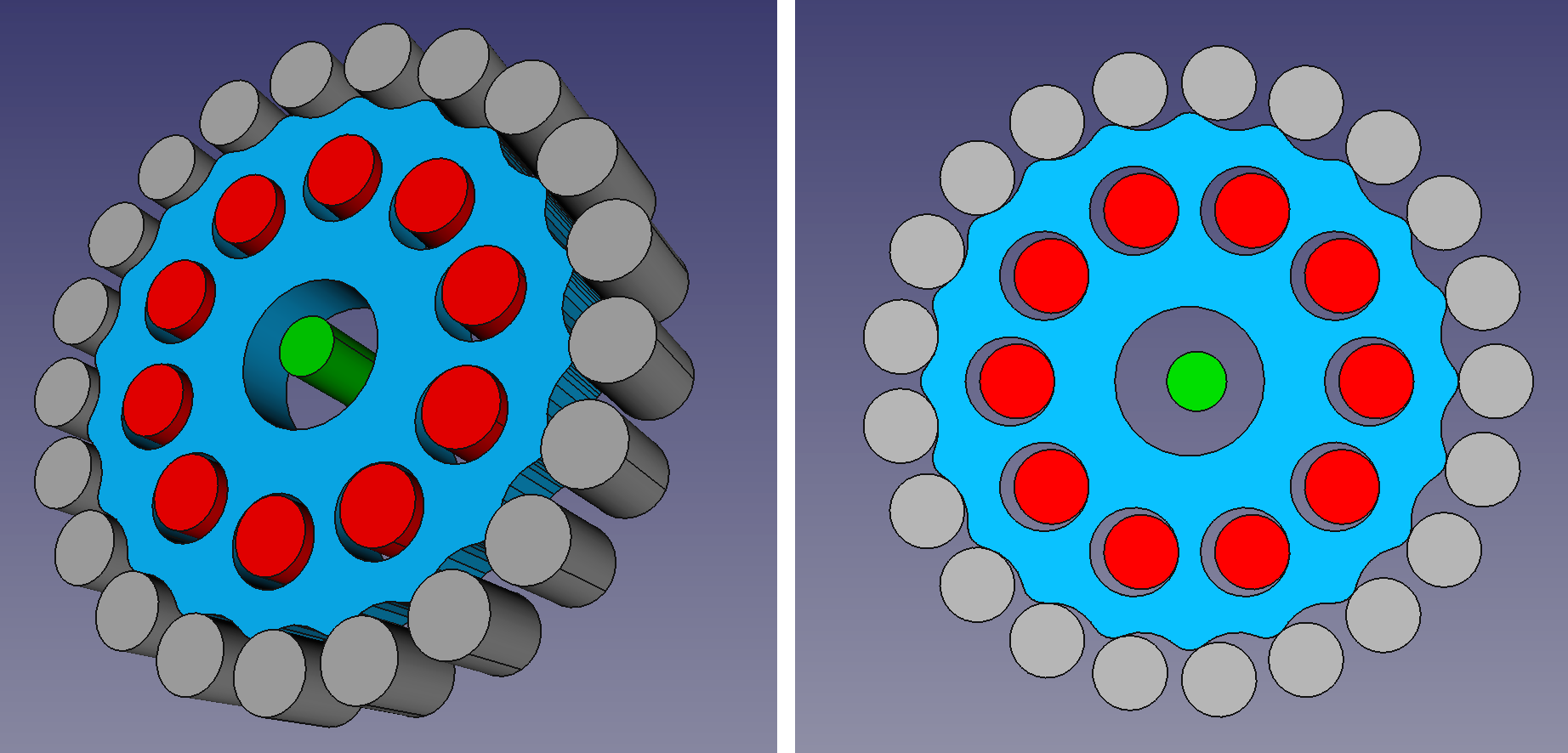
3D Printed Cycloidal Gearboxes RepRap Ltd
e - Eccentricity, or the shift of the cycloid disk's center relative to the center of the pin ring. The parametric equations generated by this calculator define an epitrochoid curve from which the actual profile of the cycloid disk (shown in red) is easily obtained using Blender's Inset tool. The inset amount equals the pin radius (d / 2).
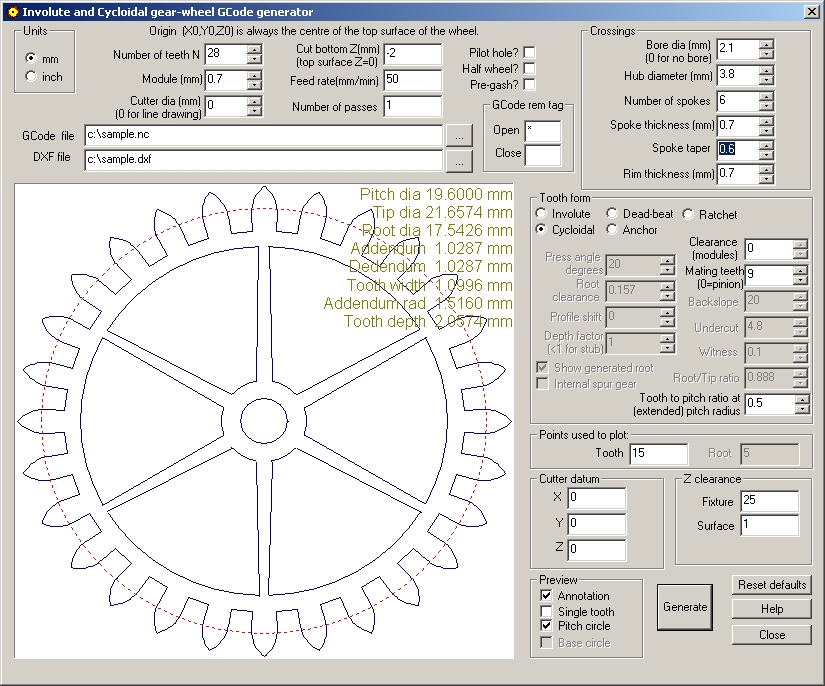
Involute and cycloidal gear designer GCode Generator
A unique principle of cycloidal gears is that the outer rolling circle used to create the addenda tooth flanks (epicycloids) on one gear is used as the inner rolling circle to create dedenda tooth flanks (hypocycloids) of the other gear. This ensures a constant angular velocity and holds up the fundamental law of gearing, which states that the.

How do cycloidal gears work and where are they used?
Cycloid gear online calculator. The tooth profile is a general term for cylindrical gears of various cycloidal lines or their equidistant curves. Cycloidal gears have few teeth and are commonly used in instrumentation and are less used as power transmissions. Its derivative type cycloidal pin wheel drive is used more.